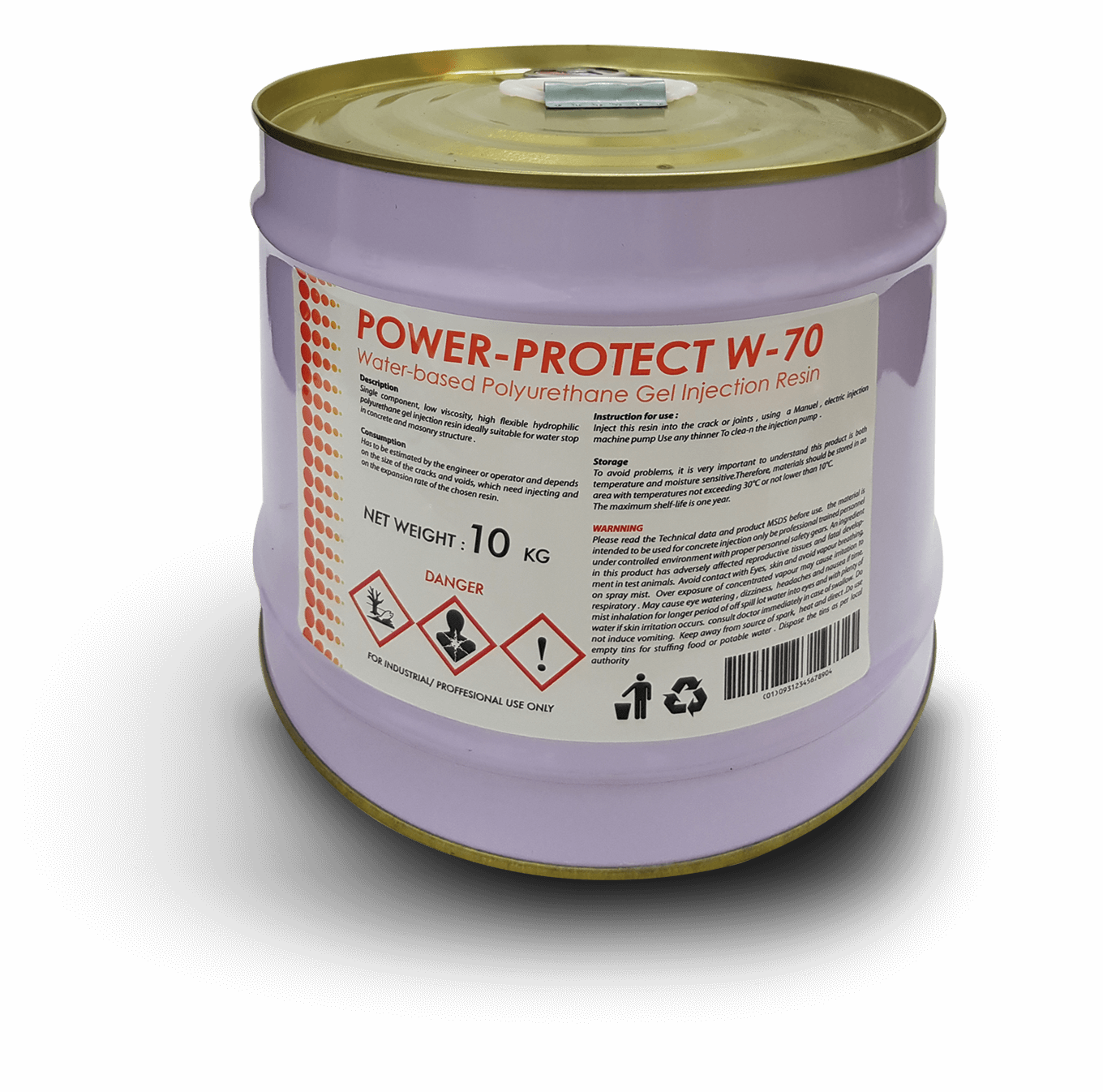
POWER-PROTECT W-70
POWER-PROTECT W-70 is an Water-based Polyurethane Gel single component Injection Resin
Description
Single component, low viscosity, high flexible hydrophilic polyurethane gel injection resin
Applications
It can stop the water leaking in the building very fast, widely used in :
Subway Station, Tunnel, Culvert, Foundation Improvement, Soil Settlement, Reservoir, Port Project, Top Slab, Cracks Construction Join, Shrinkage Crack, Basement hairline crack etc.
Test Report
Item | Standard Index | Test Results |
---|---|---|
Density (g/cm3 25℃±0.5℃) | ≥1.00 | 1.07 |
Viscidity (Mpa.S 25℃±0.5℃) | ≤1.0×103 | 300 to 600 |
Gel Time /s | ≤150 | 10 to 130 |
Foaming Capability /% | ≥350 | 350 |
Non-Volatile Content/ % | ≥75 | 80 |
Flash Point ℃ | ≥124 | 160.6 |
The ignite Temperature ℃ | 402 |
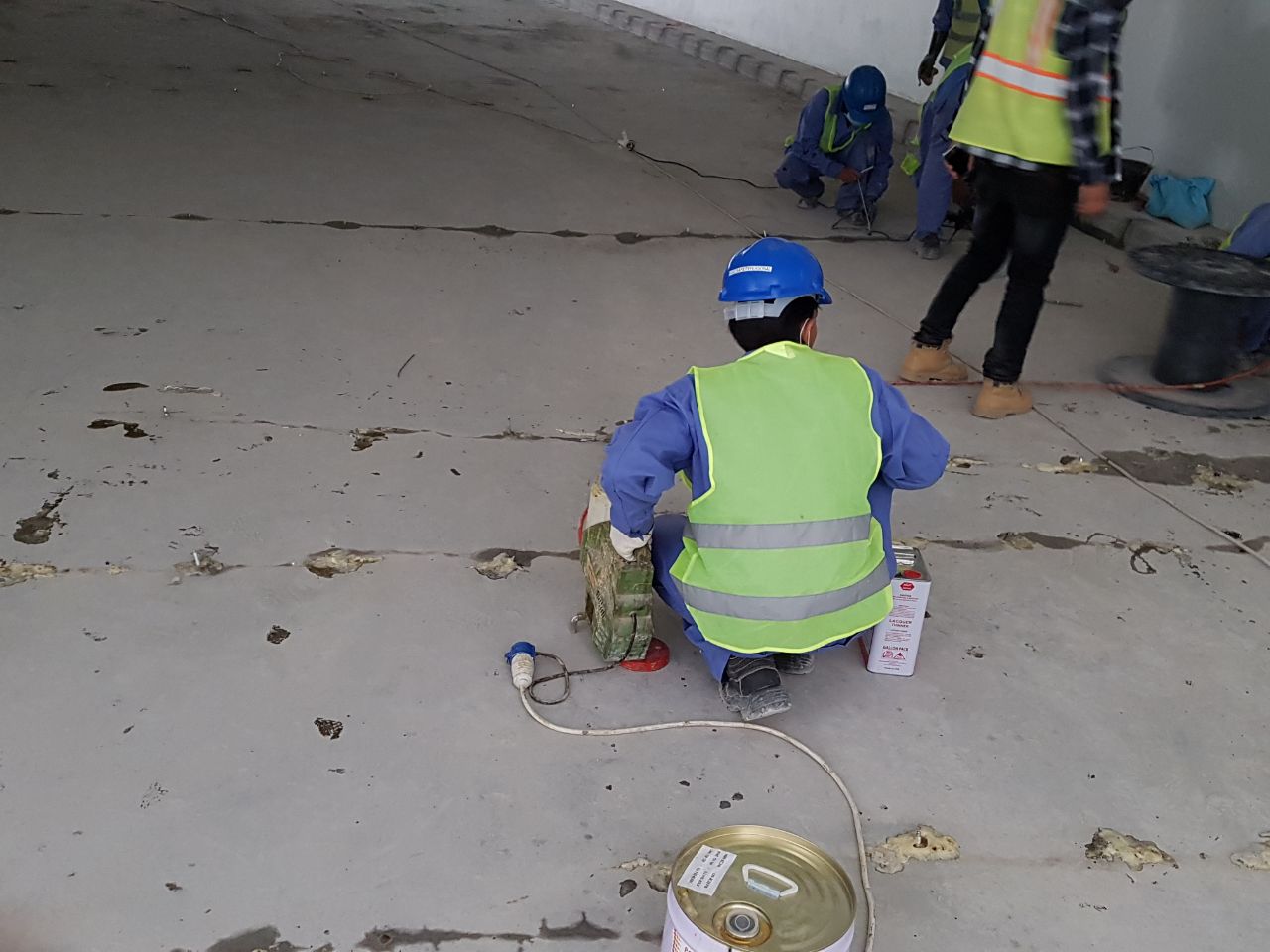
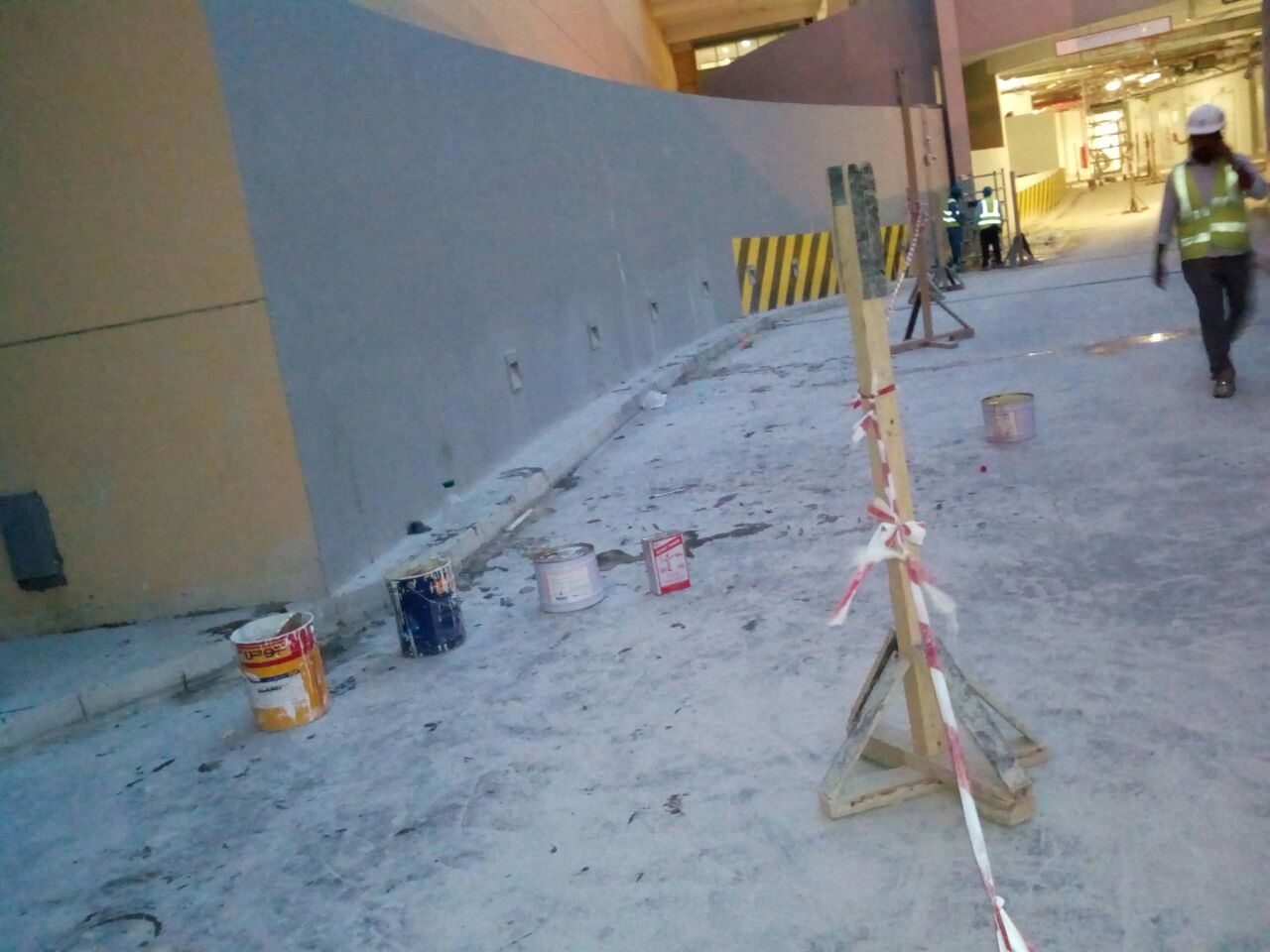
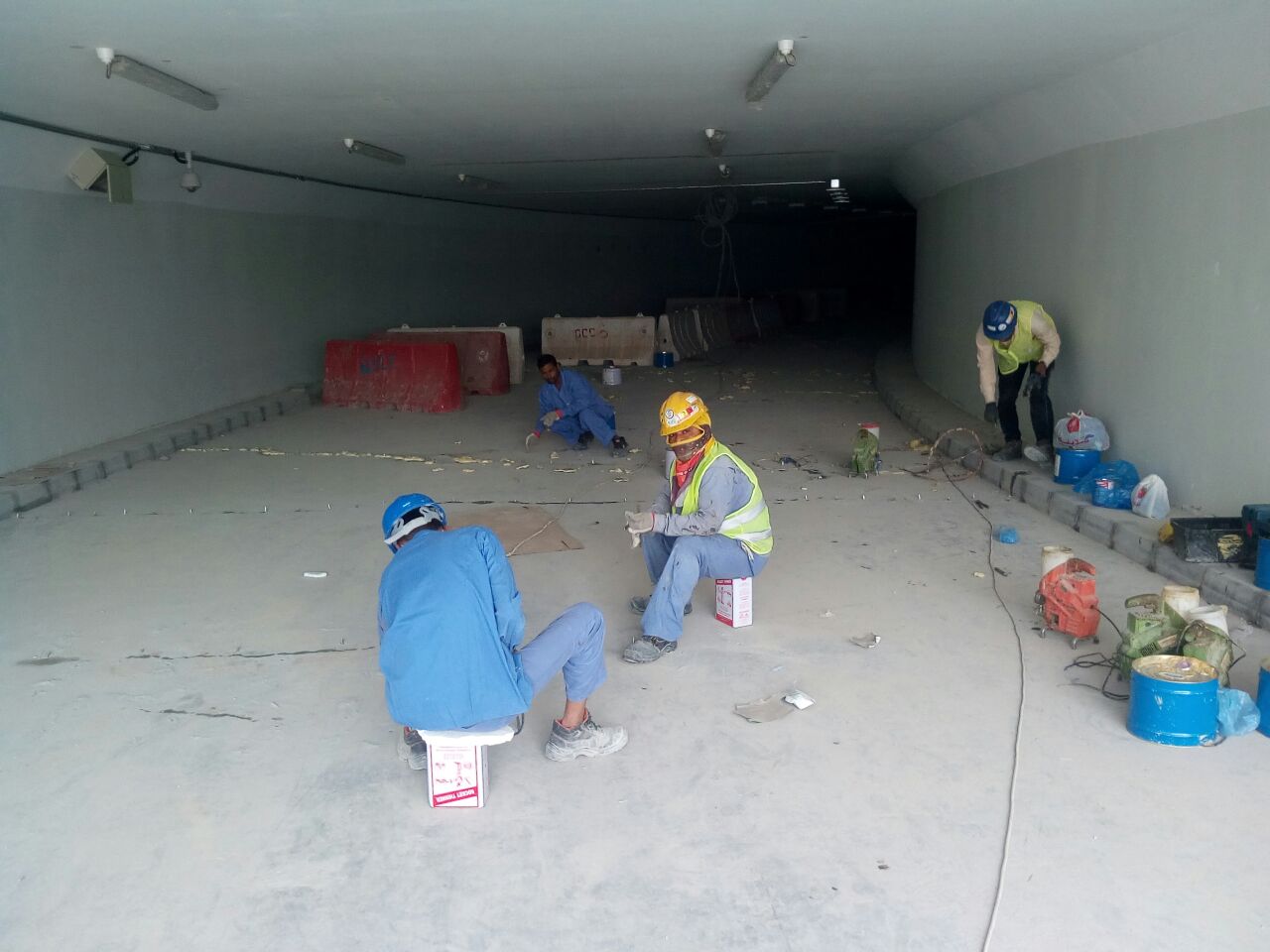



Usage
Hairline cracks are defined as cracks less than 1.5mm. These cracks can be the most difficult to seal as it is tough to force a thick resin into a tight crack. This situation are suitable to use “Power-Protect W-70 ”. Joints are easy to seal if you know the proper procedures. “Power-Protect W-70”, while great in tight cracks, works as well as sealing wide cracks
Consumption
Has to be estimated by the engineer or operator and depends on the size of the cracks and voids,which need injecting and on the expansion rate of the chosen resin.
Advantages
- Low viscosity
- Adjustable set time-as fast as 20 seconds
- Water impermeable
- Injected as a single component, direct use without to mix extra catalyst
- Used for injecting cracks widths from 0.2 -10 mm.
- Suitable for hairline Cracks .
Cleaning
•Resins must be cleaned up immediately before it sets.
•Packers must be removed within 24 - 48 hours and patched with appropriate epoxy mortar .
•Electrical grinder can be used to remove excess cured resin that flowed out the cracks.

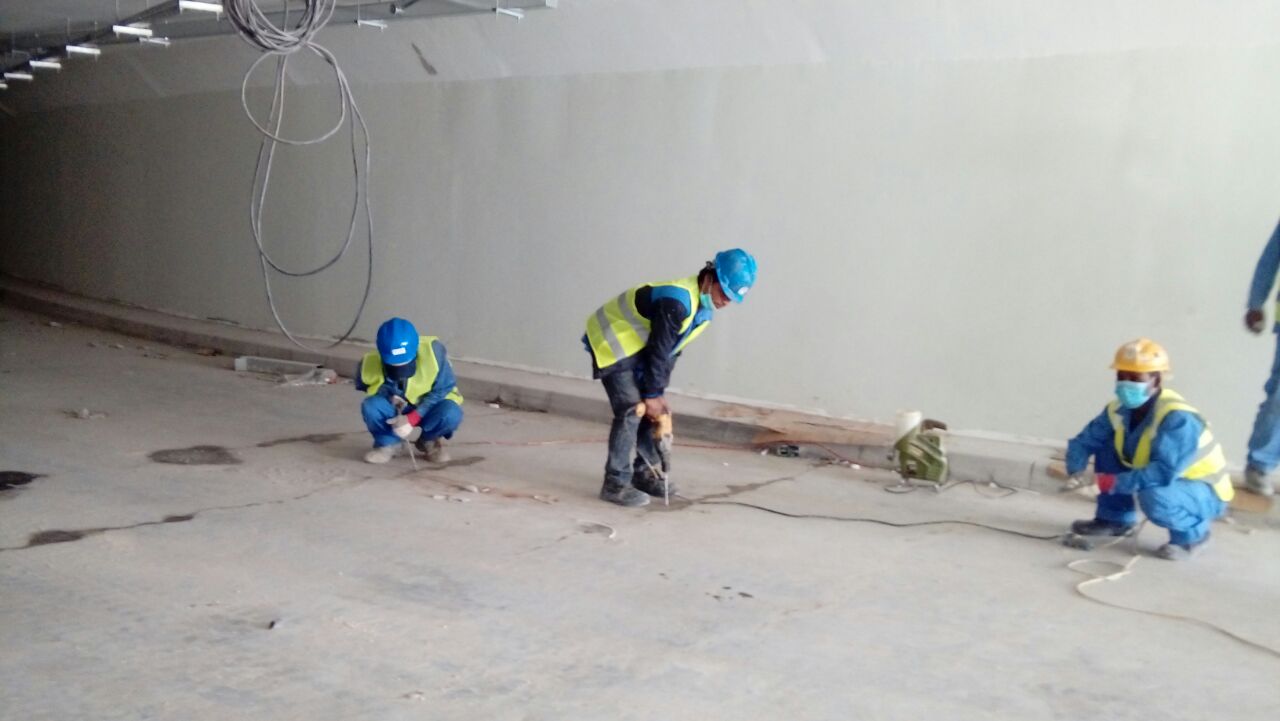
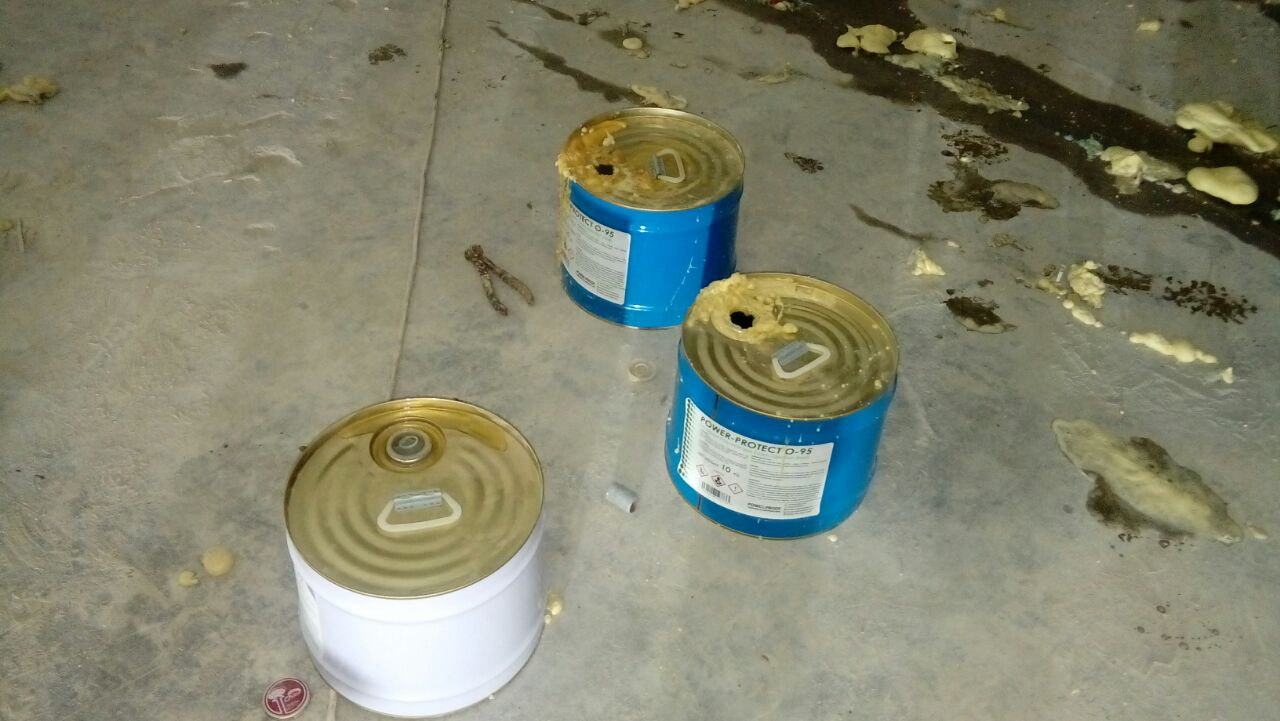
Packaging
Power-Protect W-70 is available in 10 KGS Special Iron Pails
Preparation
If water leakage is found in the water tank or retaining wall, conduct a visual survey to locate the apparent source of the leakage. If the concrete structure is plaster all plaster should be removed from the affected area to expose the concrete below. There after mark the crack through which the water leakage is observed .
Drilling
Use a high quality rotary hammer drill to make injection holes with a varied distance from 15-50 cm to each other, according to the width of crack.
The drilling angle should be approximately 45 degrees or less to concrete surface and intersecting the crack, at a distance of ½ the depth of the concrete element from the crack.
Clean all the holes from dust using air pump.
Fixing
Install injection packers into drilled holes ensuring that top of the sleeve is just below the surface of the concrete to secure sealing of the injector.
Applying
- All it have to be done after closing the cracks with Power-Protect O-95 foaming resin .
- Power-Protect W70 is to be applied using the Injection machine (Ex. Smart X).
- Make sure that the delivery line and all the fitting are connected tightly and in new condition at all time. Also ensure that no contamination has entered the delivery system.
- Start the Injection machine with low speed to start the pumping process and increase gradually.
- Once the desired working pressure is obtained set the switch of the machine so that this pressure will both be exceeded. In a regular injection the injection pressure will be well below the 400 bar mark.
- Continue until the crack is filled completely and resin can be seen emerging from the crack surface.
- Then start the process with the next packer until all the packers are done.
- Allow curing overnight and removing the packers and close the holes with special epoxy mortar that can be applied by trowel, spatula or knife.
- If the water is seen at adjacent place 7 days later, the procedure should be repeated until the whole structure is dried.
Health & Safety
Power-Protect W-70 is classified as harmful.
Power-Protect W-70 is classified as irritant.
In case of spills and accidents, refer to the Material Safety Data Sheet of the products or when in doubt contact the Manufacturer .
Always wear protective clothing, gloves and protective goggles when handling chemical products.
For full information, consult the relevant Material Health and Safety Data Sheet.

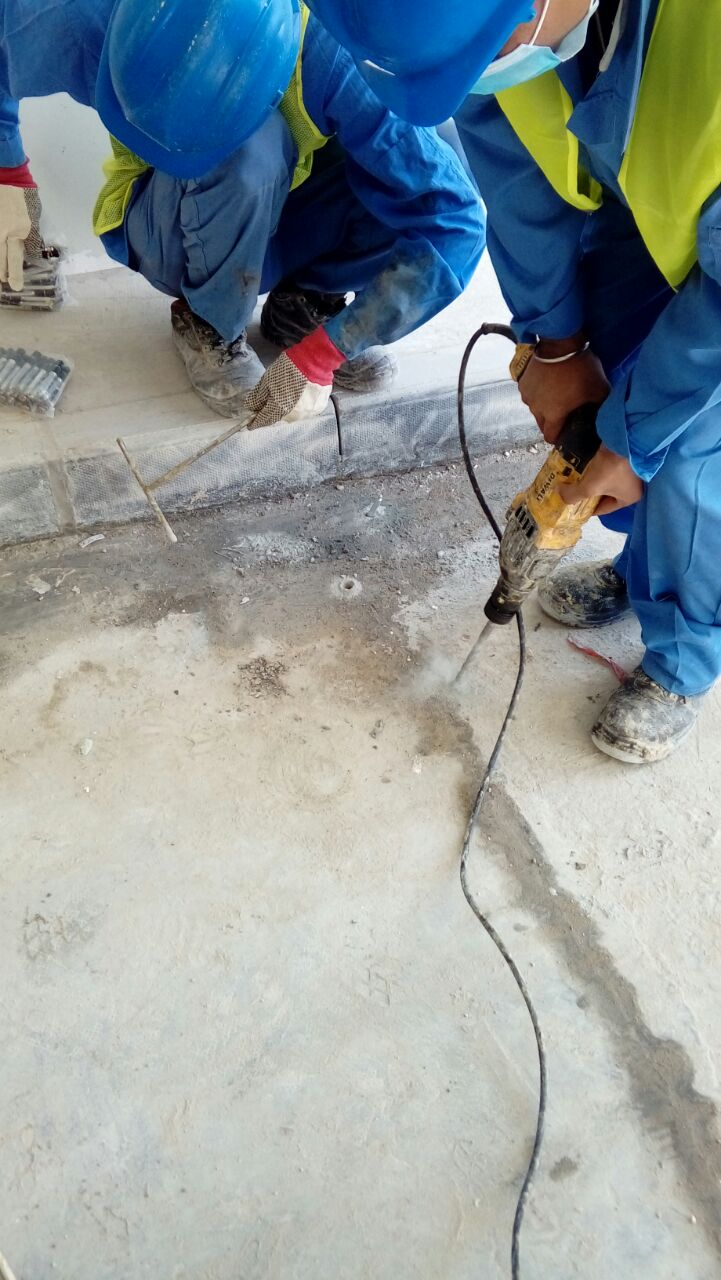
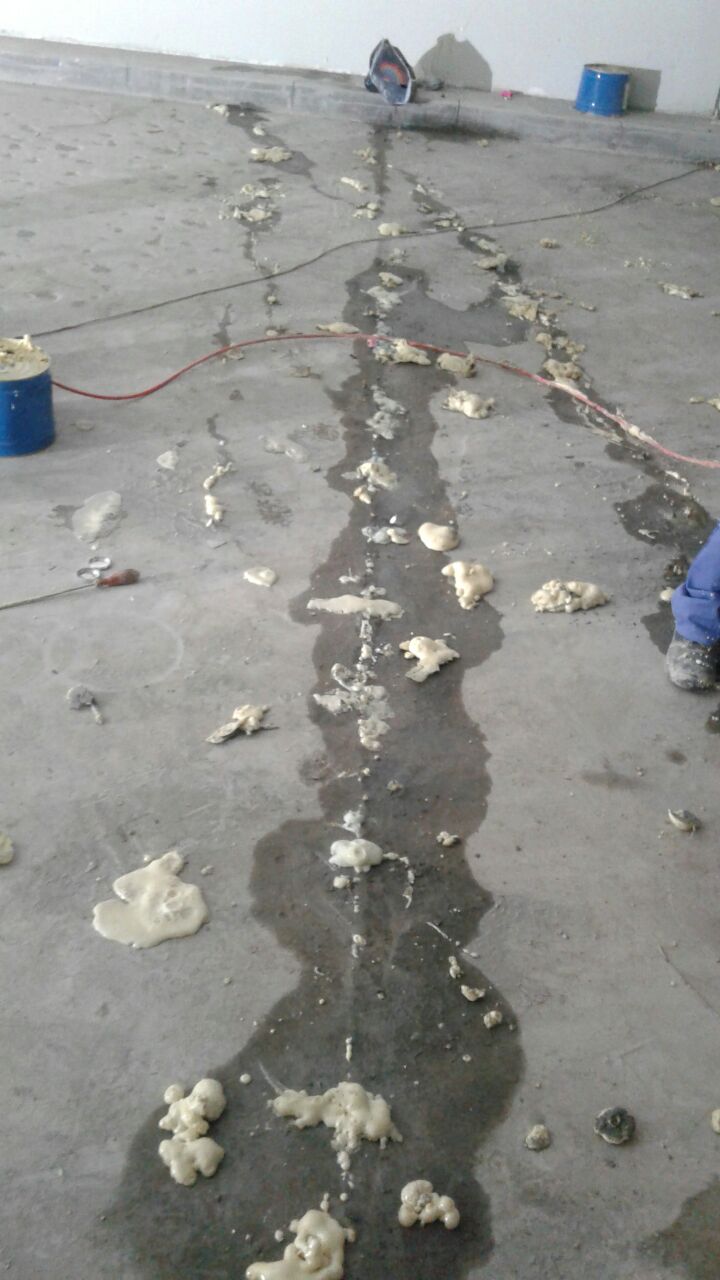
Appearance
Transparent maple liquid
Equipment
•SMART-X Integrated Injection Machine
•Compact 6 powerful Injection Machine
•SP-5 single component injection machine
•Set of Injection Packers
Storage
To avoid problems, it is very important to understand that Power-Protect W-70 istemperature and moisture sensitive.
Therefore, materials should be stored in an area with temperatures not exceeding 30°C or not lower than 10°C.
The maximum shelf-life is one year.